Products Used | ApronSeal™ Double Skirting , Dust Curtain , External Wear Liner , Martin® Modular Chute Wall , Tail Sealing Box , Trac-Mount™ Idler |
---|---|
Product Types Used | Dust Management and Containment Solutions , Transfer Point Solutions , Belt Sealing , Belt Support , Dust Containment |
Solutions | Installation |
Industry | Pulp and Paper |
Customer | Paper Plant in Southern US |
Problem

The pulp and paper plant was having trouble with fugitive material accumulating on the structure, catwalk and the ground from their current transfer point blowing wood dust out of the end. Air velocity readings were also reporting less than desirable readings of 1400 CFM. Among these issues, the biggest problem was dust and spillage.
The release of airborne dust can cause health concerns and create negative attention from regulatory agencies. Any material that spills off the conveyor is a loss - loss in material, profit and efficiency. The spillage also creates the need for manual cleanup which takes man-hours and is a dangerous task - putting workers in harm's way. Handling around 1,730,000 tons of material per year, the plant could not afford to deal with inefficient operations.
Solution
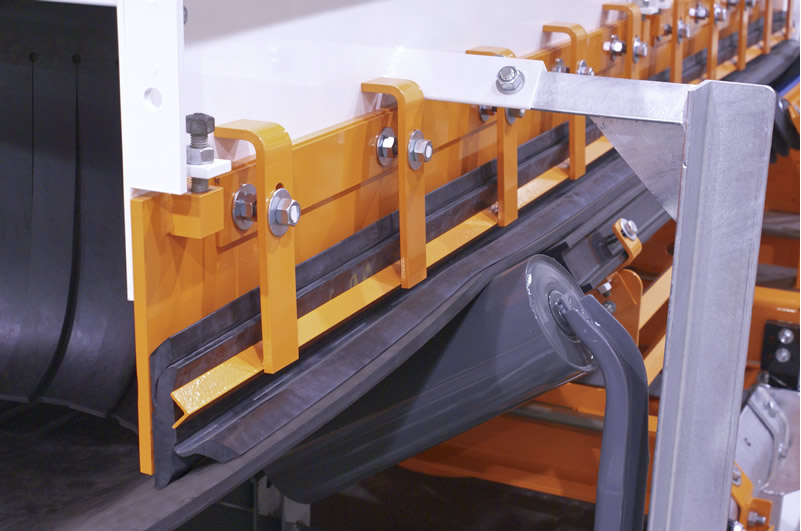
The plant was currently using an on-site contractor that did not specialize in transfer point work. They also had slider beds fabricated but they did not address the belt support problem. After inspecting the current system for opportunities for improvement, Martin recommended installing belt support and belt sealing systems to help keep material on the belt. Martin supplied EVO® External Wear Liner, Martin® ApronSeal™ Double Skirting, impact and non-impact Martin® Trac-Mount™ Idlers, EVO® Modular Chute Walls, multiple Martin® Dust Curtains and a Martin® Tail Sealing Box. One of the last upgrades Martin made was installing an all-new standard transfer point.
Results
The plant is pleased with its recent improvements performed by Martin Engineering. Air velocity ratings at the exit of the new zone now produce results at 110 CFM. According to plant personnel, "you could barely feel any air coming out of the end. Martin sealed up the entire load zone, preventing any spillage and there is no more dusting present at all."
In a recent follow-up visit conducted by Martin's salesperson, the plant confirmed that the new transfer point system and other upgrades successfully resolved all of their issues.
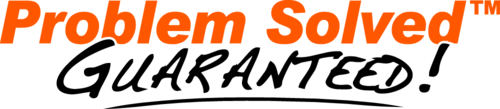
We've solved your problem somewhere before!
While your problem seems unique and frustrating, with 70+ years of solving similar problems around the world, and with the most experienced and educated people on our teams, we can assure you that we’ve “Been There, Done That.” At least close enough to know what needs to be done next and adjust for your situation.
Put Us To The Test For Free! Let Us Give You a Solution.