Products Used | Air Cleaner , ApronSeal™ Double Skirting , Slider Cradle |
---|---|
Product Types Used | Dust Management and Containment Solutions , Transfer Point Solutions , Belt Sealing , Belt Support , Dust Filtration |
Solutions | Installation |
Industry | Coal-Fired Power |
Customer | Orlando Utilities (SEC) Orlando, FL |
Problem
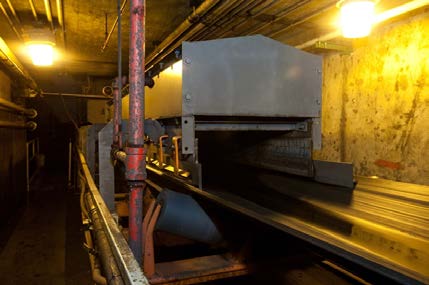
Orlando Utilities Commission – Stanton Energy Center (SEC) is one of Central Florida’s leading environmental stewards, meeting or exceeding all air permit limits with advanced pollution control equipment. When company officials decided to upgrade the dust containment on one of its primary coal conveyors, they contacted Martin Engineering. They wanted to increase the safety aspect by limiting dust and spillage from one of its principal conveyors, engineers wanted to reduce airborne particles and eliminate a potential source of trips and falls. They also wanted to reduce clean-up and maintenance time, allowing critical manpower to be utilized elsewhere and improve plant efficiency. Additionally, preventing coal dust spillage would help minimize wear on rollers and other moving components, saving on replacement part costs and labor.
Solution
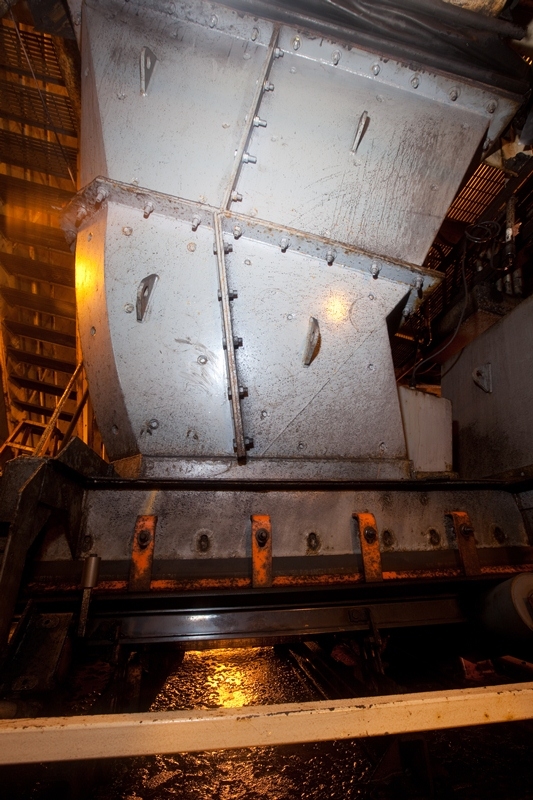
To address the situation, Martin supplied and installed a number of upgraded components, including Martin® Double ApronSeal™ Skirting, which employs two wear surfaces on a single elastomer sealing strip installed along the bottom of the skirtboard in the loading zone. Martin also installed an impact cradle to better absorb the force of the falling material and protect the belt and structure. In Addition, a Martin® Slider Cradle was added under the skirt board to better support the edges of the belt and eliminate sagging. To maintain precise centering, Martin installed a belt tracking system for immediate, precise adjustment.
Finally, Martin installed a high-efficiency insertable air cleaner with an explosion-proof motor. The Martin® Air Cleaner can eliminate many of the problems seen with central “baghouse” collection systems; they help solve airborne dust problems by keeping fine particles in the load or returning them to the material stream.
Results
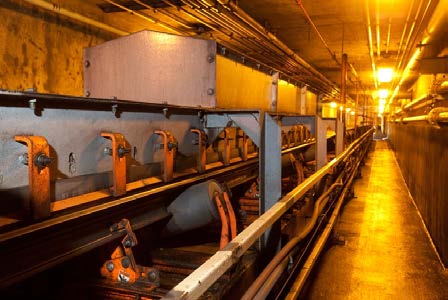
The improvement was immediate. “It’s not just the savings in cleanup time, but also in preventing the idlers from wearing our prematurely. Now I don’t have to send my guys out there to replace those failed components, so it saves on labor and replacement parts, as well as the housekeeping time,” said Material Handling Supervisor Stuart Cason. “No question the system has paid for itself. We used to spend a lot of time making adjustments and repairs, but since the install, the system has been essentially maintenance-free.”
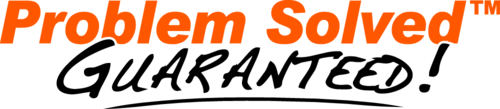
We've solved your problem somewhere before!
While your problem seems unique and frustrating, with 70+ years of solving similar problems around the world, and with the most experienced and educated people on our teams, we can assure you that we’ve “Been There, Done That.” At least close enough to know what needs to be done next and adjust for your situation.
Put Us To The Test For Free! Let Us Give You a Solution.