Products Used | DT2S Reversing Cleaner , DT2H Reversing Cleaner XHD , QC1™ Cleaner HD , SAF2™ Cleaner |
---|---|
Product Types Used | Belt Cleaning Solutions , Primary Belt Cleaners , Secondary Belt Cleaners |
Solutions | Installation |
Industry | Mining |
Customer | La Quinua Agglomeration Plant, Newmont Mining Corp. Minera Yanacocha, Peru |
Problem
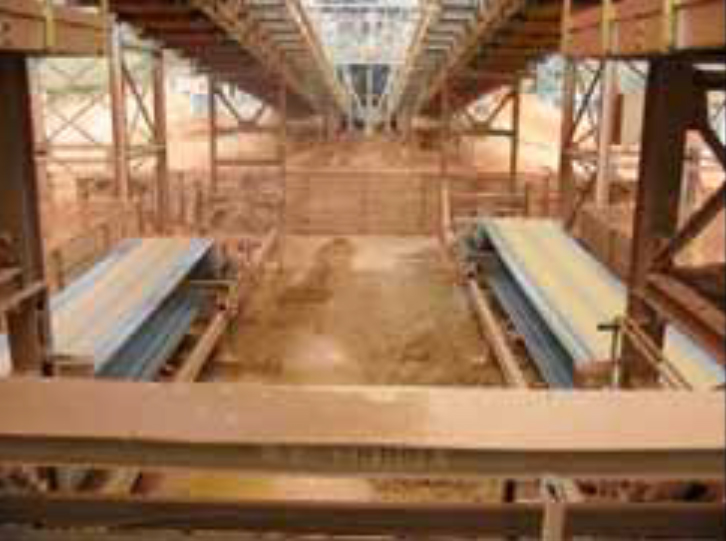
Plant management wished to compare the performance of competitive belt cleaning systems.
Solution
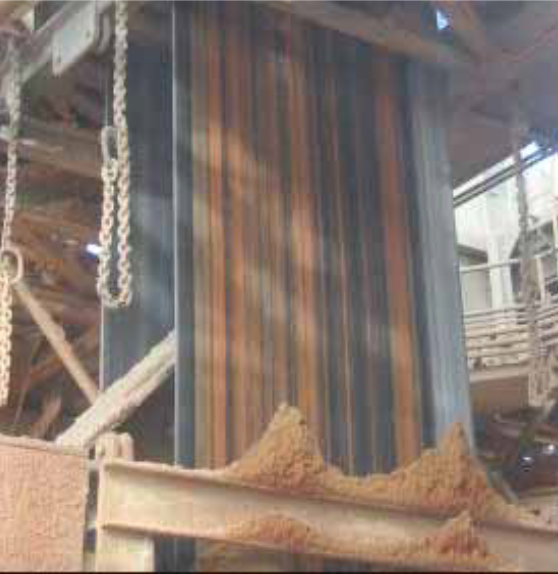
The plant operates parallel (redundant) conveyor systems that carry approximately the same material load on the same operating schedule. Installing competing belt cleaners on the side-by-side conveyors allowed the plant to compare belt cleaning results. A Martin Engineering belt cleaning system was installed on Belts #1 and #2 North. On Belt #1 North, this system consisted of a Martin® QC1™ Cleaner HD, a Martin® SAF2™ Cleaner, awater spray bar, a Martin® DT2 Cleaner and a Martin® DT2 Inline Cleaner XHD.
All three of the secondary cleaners incorporated tungsten carbide blade tips. Comparable belt cleaning systems supplied by a competitor were installed on Belts #1 and #2 South. Tests were conducted to analyze the amount of carryback remaining on the belts after the belt cleaners were installed. In these tests, a putty knife is held against the moving belt for ten seconds to remove residual material. The material removed is then weighed, and this amount is multiplied up to provide the amount of material left remaining on the belt during a day of operation.
Results
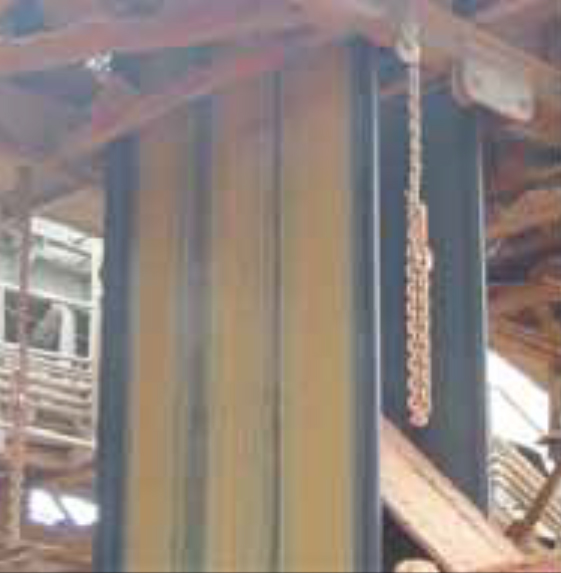
The Martin Engineering Belt Cleaning System installed on Belts #1 and #2 North (above top) removed more residual material than the competitive cleaners installed on Belts #1 and #2 South (above bottom).
It was calculated that the belt cleaners from Martin Engineering left approximately 28.5 metric tons of material on Belt #1 North over 24hours of operation. The testing showed the competing belt cleaning system on Belt #1 South left 171 metric tons of material in 24 hoursof operation. On the surge pile conveyors—Belt #2 South—the competing cleaner, left 23.8 metric tons of material as estimated over a 24-hour period.
The Martin® Belt Cleaners left only 5.15 tons of material over the same period on Belt #2 North. The test report noted that neither cleaner could remove 100% of the materials due to excessive wear and damage in some areas of the conveyor belt. Based on the test results, Martin Engineering’s representative in Peru recommended the adaptation of the same Martin® Multiple Cleaners on all conveyors in the plant.
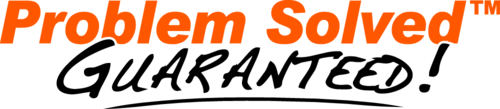
We've solved your problem somewhere before!
While your problem seems unique and frustrating, with 70+ years of solving similar problems around the world, and with the most experienced and educated people on our teams, we can assure you that we’ve “Been There, Done That.” At least close enough to know what needs to be done next and adjust for your situation.
Put Us To The Test For Free! Let Us Give You a Solution.